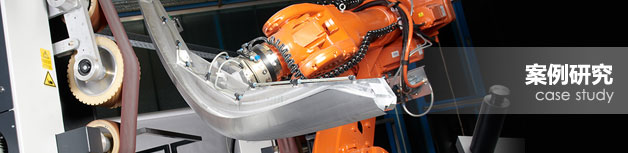
-
Wax welded group tree - Think-Automation robotics
Lost foam casting usually adopts the wax method or foam model method. Due to the mass production of convenience and accuracy and consistency, lost wax casting method is widely used in precision casting industry. With the popularization of robotics and automation systemdeeply, disappear of robot automation application technology of casting field has widely beenmature: such as slurry dipping, sandblasting, shear gate, repair burrs. In the job requires high precision, large workload before the wax pattern welding group of trees, cleaning process,many enterprises still use the traditional manual welding group tree technology.
This case is Shanghai Xin Zhi KUKA robot automation in Jiangsu of a foundry provides a welding group tree production line. In the user within the plant, originally need every dayabout 1800 wax bonding work 4 skilled worker is completed, through automation wax group tree transformation after the robot, completed by the KR6 R900 to 2 KUKA robots in thepremise of existing efficient, can greatly improve the consistency of welding, for the broadpromotion space for expanding production capacity.
[preliminary scheme demand and Think-Automation users to provide]
The use of automation system to replace the artificial completed wax welded and gate stickgroup tree work, not only to ensure the welding quality, but also as far as possible to reducethe error rate.
Process: wax press wax pattern "cooling" gate stick material positioning "wax welded group tree" overhaul "wax tree parts cleaning, drying" pendant turnover.
Product types: about 10 types, size and group tree form were different, as far as possible to meet the flexible manufacturing switching between different batches.
The ratio of input and output requirements: Transformation of the former 2 groups of 4artificial 8 hours a day bonding is completed about 6000 pieces of wax. Automated transformation to meet at least the existing capacity, and makes the equipment investment cost controllable system.
According to user needs, taking into account the traditional manufacturing non-standardautomation equipment design and high cost, and the production of flexible low, Hin Chi company offer to achieve the above wax welded group tree operations used by the robot, andrecognized by users. In the investment cost of the equipment, the preliminary investmentestimate of about 800000, is also within the scope of the basic client bear. Therefore, the project soon entered the key experimental demonstration of the development of investmentbefore the.
[wax experiment and improvement of welding robot]
The experimental phase: artificial by soldering machine.
Feasibility: poor.
Cause analysis: iron drainage mechanism and robot bonding wax with action difficult, difficult to harmonize, iron cleaning work automation transformation of inconvenience.
Experiment two period: the robot using heater heating wax after welding.
Feasibility: poor.
Cause analysis: lack of timely corrective deviation robot such as flexibility and operation of artificial in action, leading to weak welds, the welding deformation and other substandard goods increased.
Experiment three period: robot using bonding welding wax wax.
Feasibility: the more feasible.
Details that need improvement: adhesive wax dripping, transition arc weld bonding.
Improved process details after the experiment: the basic meet user quality needs.
[the design phase of the project problems and solving proposal]
Clip question 1 wax and gate stick:
The first gas claw clamping scheme in the actual welding mechanical interference occursduring the operation, easy to damage the wax, and the distance from the weld position andclamping position too close easily lead to decline in the quality of welding and toolingpollution, so through the act with united strength Think-Automation and user sides, throughturns improvement, and ultimately using gas claw clip + vacuum adsorption double grip fit way, can effectively solve the key problem.
As a problem of precise positioning of the 2 gate stick:
Think-Automation for the user the main products of the runner bar shape and a plurality ofwax verticillate group tree configuration characteristics, design of servo positioner, gate stickby the robot clip positioning after placed in the positioner mechanism, collaborative positionerand servo robot system, in accordance with the procedures set rotating displacement.
The construction of processing 3 wax small tail:
Wax wax press press with a "tail", Think-Automation the design of the pneumatic scissors for it, to build before adhesion.
The cleaning problem 4 wax welded group behind the tree:
The whole system includes the wax cleaning special cleaning groove, a drying groove. Tree structure robot grasping welding group tree complete active cleaning, drying operation.
More than 5 batches of flexible production switching problem:
System for most batches of product design verticillate group tree structure, which can meet the production of the main category, otherwise individual special structure, group numberstructure of small quantities of the need to separately by artificial completed.
Automatic connection problem 6 before and after the process:
Wax wax after mechanism, need to go through a period of cooling, Think-Automation design of water-cooled rapid cooling device, can have the robot directly from the wax press out after entering the subsequent operations, can also be according to the material to enter from the external needs of production.
Group tree piece structure air drying, by the robot hung on the turntable, the future will be connected to enter into the subsequent operation suspension chain. Now there is artificial thesuspension frame transfer to other stations for subsequent leaching slurry blasting operations.
[the case final delivery robot welding group wax tree production line configuration]
1, 2 sets of PC based Windows control of KUKA robot KR6 R900 control system, the robotbelongs to the innovation of KUKA modeling: high speed, agility, small space, low power.
2, the robot hand grasping: pneumatic clamping jaw and the vacuum sucker.
3, stick gate positioning fixture and servo positioner;
In 4, resection of the tail of the special wax pruning mechanism;
- News
-
casting robot application case -- wax group tree welding automation
This case is Shanghai Xin Zhi ...